Thermal interface material (TIM) is the generic term for materials inserted between the power module and the heatsink to improve their thermal connection. TIMs can also be referred to as thermal paste, thermal grease, or phase-change materials.
The thermal interface material is essential as IGBT- or MOSFET-based power modules can produce considerable losses. Its primary purpose is to provide a thermal interface between the power module’s DCB (direct bonded copper) and the heatsink. It does so by evening out surface irregularities and establishing a metal-to-metal contact wherever possible, thereby ensuring optimal cooling. Because the thermal conductivity of TIMs is much lower than that of the heatsink, the DCB, and the semiconductor, the TIM layer has to be as thin as possible.
Contents
- Thermal Interface Materials (TIM)
/ What is thermal paste / thermal grease?
/ How to apply thermal paste / thermal grease?
/ Pre-applied thermal paste / grease options for MiniSKiiP power modules
- The benefits of HPTP
- What are the benefits of pre-applied thermal grease? - Phase-change material options for power modules at Vincotech
/ What is a phase change material?
/ What are benefits of PCMs?
/ Pre-applied phase-change material (PC-TIM) options for power modules - Protection of thermal interface material
/ ProCap 0 and ProCap 1
/ Protection Foil - Related documents on thermal interface materials
Thermal Interface Materials (TIM)

What is thermal paste / thermal grease?
Thermal grease, also known as thermal paste or thermal conductive paste, is a thermally conductive compound that is often also an electrical insulator.
The two main components that make up thermal grease―and most thermal connection devices―are a polymer base commonly called a 'matrix', and a liquid or micronized metal filler. The ratio between these components dictates the grease’s thermal properties.
How to apply thermal paste / thermal grease?
While brushes or rollers are widely used to apply thermal grease, silk-screens and stencils result in the best thermal paste pattern, due to their ability to more accurately account for the shape of the power module’s underside. Vincotech provides dxf drawings to customers interested in applying their own thermal interface material in production.
Pre-applied thermal paste / grease options for MiniSKiiP power modules

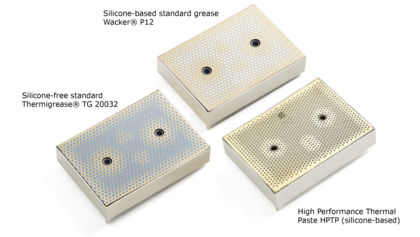
Vincotech MiniSKiiP power modules are optionally available with pre-applied thermal grease. They offer many advantages, measurable both in terms of performance and reliability. The grease is printed onto the surface using a silk-screen technology to achieve a consistently thin layer of material that conducts heat as efficiently and effectively as possible.
Depending on the specific requirements, Vincotech offers silicone-based Wacker P12 standard grease or silicone-free Thermigrease® TG20032 standard grease.
HPTP (high-performance thermal paste), a recent addition to Vincotech's offering, is a silicone-based thermal paste with good thermal conductivity. The paste has an improved nominal thermal resistance derived from its optimized filling degree, particle size, and particle distribution.
Thermal grease |
Thermal conductivity W/m*K | Released for Products | Option code |
---|---|---|---|
Silicone-based standard grease - Wacker® P12 |
0.81 | MiniSKiiP® | /1x/ |
Silicone-free standard grease - Thermigrease® TG20032 |
2.5 | MiniSKiiP® | /4x/ |
High Performance Thermal Paste - HPTP (silicone-based) |
2.5 | MiniSKiiP® | /5x/ |
The benefits of HPTP:

- Outstanding thermal performance
- Up to 40 % lower thermal resistance Rth(j-s) than standard thermal grease
- More output power or longer lifetime
What are the benefits of pre-applied thermal grease?

- Lower handling costs and less production overhead with no need for screen-printing equipment
- Automated screen-printing for utmost precision and reliability
- Thinnest thermal grease layer for minimum thermal resistance and maximum thermal conductivity
- Extended lifetime and enhanced reliability
Phase-change material options for power modules at Vincotech

What is a phase change material?


There are considerable benefits to using a phase-change material (PCM) to increase the thermal conductivity between the module and the heatsink. PCMs are solid at room temperature and transition to a liquid state at temperatures above 45 °C. This makes them smear-resistant during transportation and module assembly.
What are benefits of PCMs?

- Up to 20 % Rth reduction from Tj to heat sink for Al2O3-based modules
- Up to 30 % Rth reduction from Tj to heat sink for AlN-based high performance modules
- More output power or longer lifetime
- Standard solder profile applicable (e.g. J-STD-001, J-STD-003)
- Compatible with Press-fit pins
Pre-applied phase-change material (PC-TIM) options for power modules

Vincotech power modules are optionally available with pre-applied phase-change material. Our in-house screen-printing process ensures that the material’s thickness is configured and optimized for maximum heat transfer capability. The phase-change material is released for all flow housings with and without baseplate in combination with a Al2O3 DCB, and for MiniSKiiP® modules with a Si3N4 DCB.
Vincotech offers two different types of pre-applied phase-change materials:
Parameter | PSX-P7 * | PTM6000HV | Unit |
---|---|---|---|
Option code | /3/ | /7/ | |
Thermal conductivity | 3.4 | 5.2 | W/(m*K) |
Phase change temperature | +45 | +45 | °C |
Max. operating temperature | 105 | 150 | °C |
Specific gravity | 2 | 2.6 | g/cm² |
* Also known as Loctide-TCP4000-PM
Protection of thermal interface material

During transportation, the thermal interface material (TIM) of modules, which are typically only semi-assembled, can be smudged, scratched, or even contaminated by swirled particles or dust. Moreover, during assembly, the thermal interface material (TIM) can be contaminated by particles in a wave soldering oven or smeared by the curtain at its exit. To protect the thermal interface material during and after PCB assembly, Vincotech has developed protection caps and protection foils.
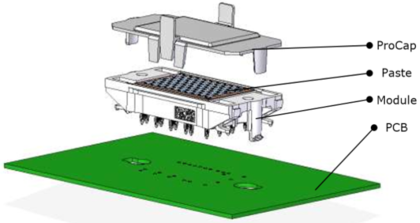
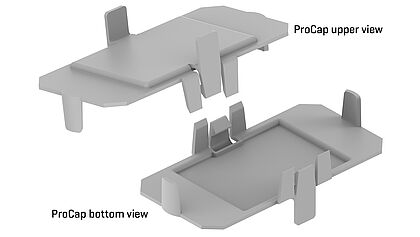
ProCap 0 and ProCap 1

ProCaps (short for Protecting Cap) are available for flow 0 and flow 1 type power modules with thermal interface materials. They can be used for both thermal grease and phase-change material.
Protection Foil

The protection foil is only available for power modules with pre-applied phase change material.
Related documents on thermal interface materials

Handling of Power Modules with Phase-Change Material
Advantages of pre-applied Thermal Interface Material
MiniSKiiP® with a Si3N4 AMB Substrate